- New contract reaffirms long-standing relationships with Abellio and with Eversholt Rail
- Derby Etches Park depot to maintain Bombardier Class 222s for East Midlands Railway mainline services until 2022
Rail technology leader Bombardier Transportation has announced today that it has signed a new Train Services Agreement (TSA) with Abellio and Eversholt Rail for the new East Midlands Railway franchise in the United Kingdom. Under the new agreement which lasts from today until December 31, 2022, Bombardier will maintain Bombardier class 222 diesel-electric multiple unit (DEMU) trains at Derby Etches Park depot for use on East Midlands Railway mainline services. The new agreement follows Bombardier’s previous role in maintaining the 125 miles per hour trains for the former East Midlands Trains franchise. The contract is valued at approximately £133 million GBP ($161 million US, €145 million euro).
Phil Hufton, President, Bombardier Transportation UK said, “We are delighted that we have reached agreement with Abellio to maintain the Class 222 fleet for East Midlands Railway’s mainline services. This important contract win is testament to our team at Derby Etches Park and their hard work and professionalism in continually delivering one of the highest performing and most reliable Intercity fleets.”
Steve Timothy, Client Relations Director, Eversholt Rail said, “We are pleased to be working in partnership with Bombardier Transportation to support the delivery of our Class 222 trains for the Sheffield – London mainline service to Abellio East Midlands Railway from 19th August”.
Under the Train Services Agreement, maintenance of the 27-strong fleet of Class 222 trains will take place at Derby Etches Park depot, where 130 staff are employed, with heavy component maintenance taking place at Bombardier Crewe.
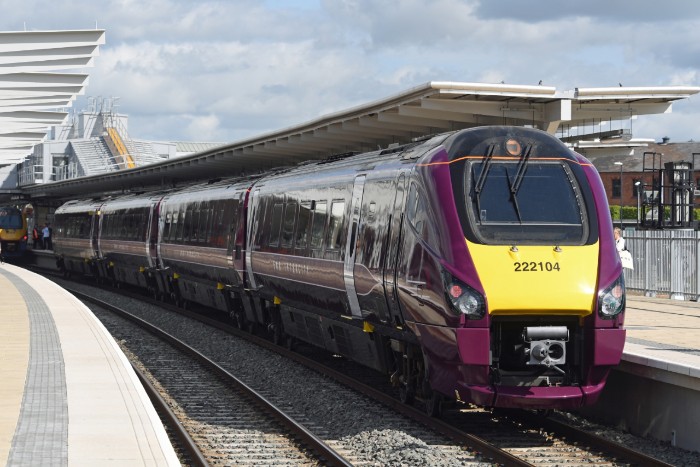