In July 1983, the OAMTC air rescue service started operations in Innsbruck with an AS355. Since then, the HEMS operator has expanded its service throughout the whole country, offering its life-saving services to the Austrian population from the mountainous regions in the west to the plains in the east near the borders with Slovakia and Hungary.
Today, OAMTC Air Rescue operates more than 22 HEMS bases throughout Austria, all named Christophorus after St. Christopher, the patron saint of travelers. Of these, 17 are in operation all year round, while four are in seasonal operation, mainly during winter, to provide HEMS services to the country’s more than 400 ski resorts. Since 1999, OAMTC air rescue has also been operating an H135 as an intensive care helicopter, which enables inter-hospital transfers of intensive care patients to the highest standards.
Relying on the H135 family since 1997
As one of the world’s first operators of the H135 family, OAMTC has relied on the helicopter as the backbone of its missions since 1997. Since then, more than 212,000 flight hours have been logged, including 1 million take-offs and landings, and more than 400,000 missions have been flown. One of the pilots who’s contributed nearly 3,000 flight hours to these impressive figures is Robert Gallmayer, who also happens to be the head of the Christophorus 9 base in the Austrian capital of Vienna. He praises the H135 for its reliability, safety and ergonomics. He also notes that Helionix, the Airbus avionics suite that’s on board the latest version of the H135, plays a big role in ensuring mission success.
There is every indication that this joint success story will continue: In 2020, OAMTC air rescue again demonstrated its confidence in the H135 with an order for five more of these helicopters, the first four of which have already been delivered to the Austrian HEMS organization.
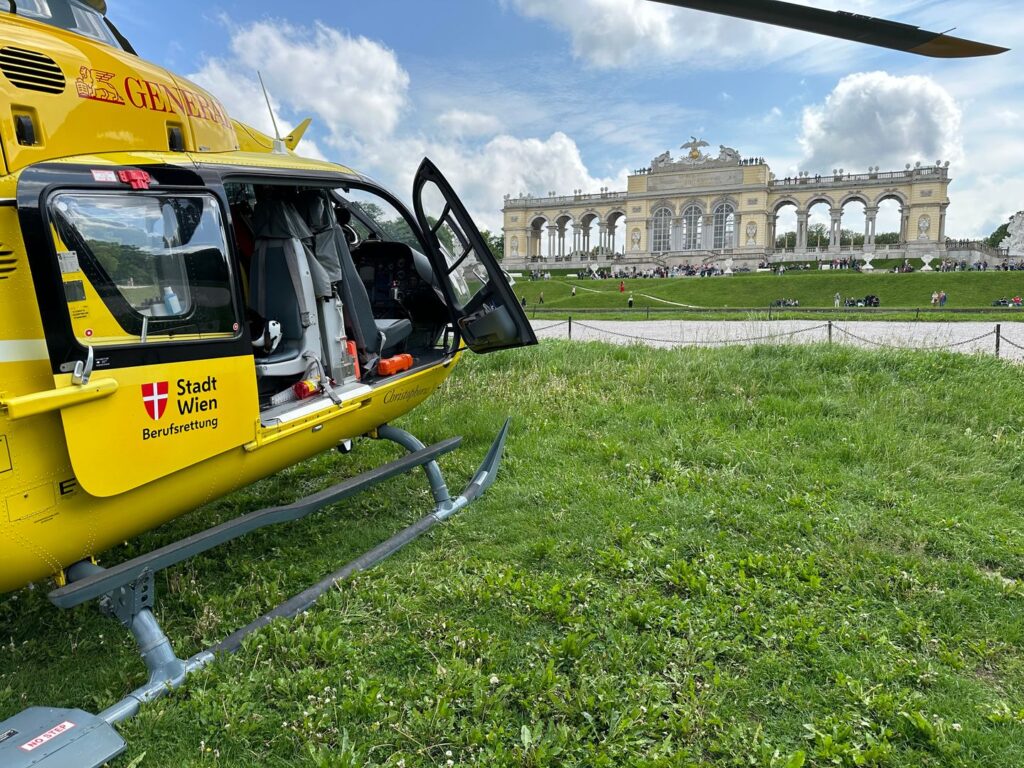