- DHL Global Forwarding opens expanded Leipzig Life Sciences & Healthcare Hub
- Frankfurt, Hamburg and Leipzig GxP facilities successfully achieve CEIV IATArecertification
- Specially trained staff and state-of-the-art equipment for storage and handling oftemperature-controlled pharmaceutical products and drugs
DHL Global Forwarding, Deutsche Post DHL Group’s air and ocean freight specialist, has expanded its Life Sciences & Healthcare (LSH) facility in Leipzig by approximately 2,500 square meters. The center is very close to Leipzig Airport and houses state- of-the-art equipment for storing and handling temperature-controlled pharmaceutical and medical products, such as vaccinations. After Frankfurt am Main, Leipzig is the second DHL Global Forwarding facility to be expanded in terms of capacity and equipment. DHL has successfully achieved IATA CEIV Pharma recertification for its GxP (good practice) facilities in Frankfurt am Main, Hamburg and Leipzig, making the company ideally prepared in Germany to meet the logistical requirements related to importing and exporting Covid-19 vaccinations.
The previous trans shipment and warehouse space of approximately 2,200 square meters in Leipzig was more than doubled when the expansion was completed in the last quarter of 2020. The second warehouse covers more than 2,500 square meters and is divided into two temperature zones. In the larger zone comprising approximately 1,700 square meters, the temperature can be regulated between 15 and 25°C. The smaller zone of around 850 square meters can be cooled down to 2-8°C. This allows pharmaceutical products to be stored at an appropriately cool temperature, to ensure their integrity. Dry ice handling for passively cooled transport containers and handling of actively cooled transport containers are also part of the standard repertoire. The immediate proximity to Leipzig Airport ensures fast import and export times. Of course, the facility also operates under the highest safety and security standards, with systems in place to immediately report temperature deviations and fire risks, as well as break-ins.
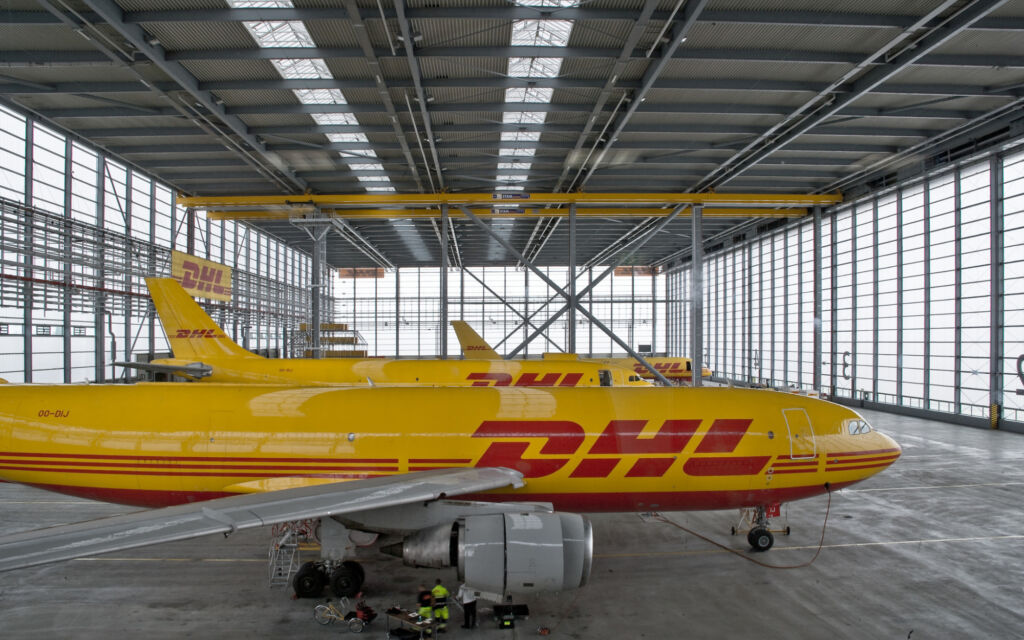
DHL and IATA are jointly committed to ensuring that the pharmaceutical industries regulatory requirements are met. A standardized approach in air freight increases productivity, accuracy, and reliability, while enabling transport in compliance with all applicable regulations. DHL began IATA CEIV Pharma certification of its facilities worldwide in 2016, raising the bar in pharmaceutical logistics. After independent third-party audits and training courses for employees on site, the DHL GxP facilities in Frankfurt, Hamburg and Leipzig have successfully renewed the quality label. DHL Global Forwarding thus enhances transportation and storage quality levels of pharmaceutical goods, and the DHL station exceeds its usual quality standards. At each location, IATA verifies compliance with its Temperature Control Regulations (TCR), the European Union’s GDP (Good Distribution Practices) guidelines, and further requirements of the World Health Organization (WHO) and other regulatory bodies.
As the leader in the life sciences and healthcare sector, DHL provides its employees, at all levels, and in all functional areas around the world, with vital tools to meet the requirements of both its customers and the supervisory authorities. For example, it provided a special training program to implement IATA regulation standards at scale in key GxP (good practice) facilities worldwide. The Certified Life Sciences Specialist (CLSS) program, offered as part of the Certified initiative, provides a comprehensive curriculum of mandatory training and specialized courses and materials to convey the knowledge needed in this highly specialized industry. As with all of DHL’s temperature-controlled locations, all employees in Frankfurt, Hamburg and Leipzig who are involved in handling life sciences and healthcare products have successfully completed the training and are certified Life Science Specialists. This ensures that sensitive shipments are handled with the utmost care and in compliance with the highest industry standards.